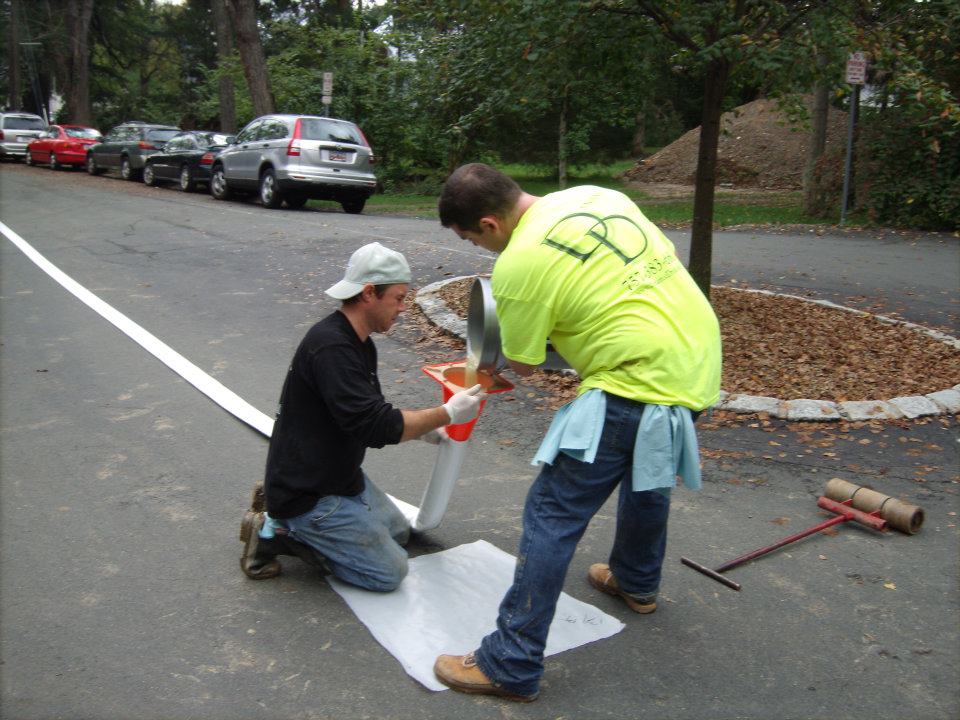
Over the last couple of months we have had several info requests on our epoxy technologies. So in order to clear up any confusion we decided to post this blog to better inform people on the different resins and epoxies we use here at Dynamic Drain Technologies. To simplify things lets break up the common sewer pipe lining job into 2 segments, lateral lining and main lining. Lateral lining being the pipe leaving a building. Main lining being the larger diameter pipe in the streets, often owned by the local municipality.
Main Lining
Traditional main line CIPP uses a vinlyester or polyester resin. This resin is designed to have more strength requirements than epoxies because the pipe is of larger diameter, deeper and carries more load like asphalt roads or parking lots on top of it. When it comes to gel times and cure times poly/vinylester resins need longer gel times so longer continuos lengths of liner can be installed from access points. We call this “pot life” in the industry. Main lining or man hole to manhole lining needs a long pot life so 500 plus feet of liner can be installed without risk of hot spots. In order to offset the long gel times with shorter cure times main lining is generally cured out with an external heat source, stream or boiling water.
Lateral Lining
Traditional lateral lining almost always uses a 100% solids epoxy resin. This resin is designed to give off no odor and be used without an external heat source if needed. The epoxy has a much shorter pot life and can be cured ambiently within hours. The pot life can be much shorter than main line resin because the pipe is half the diameter and half as long. This resin is formulated to mix onsite and can be used inside facilities. We also can control the lengths of the epoxy’s pot life based on application. We have the ability to use external heat as well if the job calls for it.