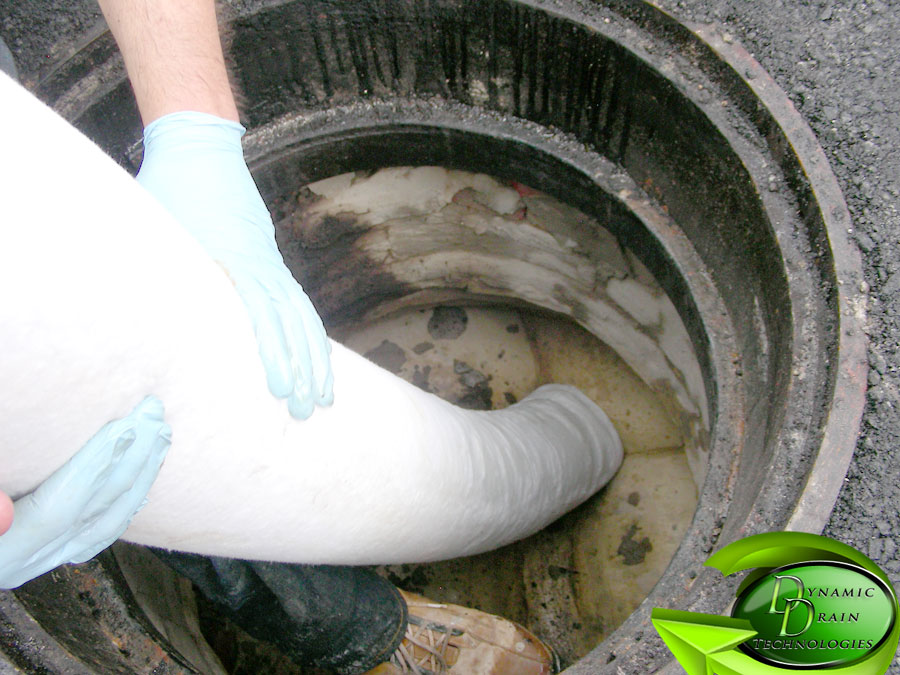
Virginia Beach Pipe Repair
CVS is opening up a brand new store in Virginia Beach on Indian River Rd. The foundation had been set, parking lot finished and the walls, windows and electricity were being installed. Then came the bad news. Unfortunately the ductile iron pipe that was used for the sanitary sewer systems had been identified as not having the correct specifications required by the International Plumbing code.
That’s where we come in! East West Construction gave us a call and contracted us out to re-line the iron pipe with our trench-less cured in place pipe (cipp) repair technology.
Preparation
First we had to prepare the liner for the pipe by measuring the liner, the pull-tape and the calibration tube to match the pipes. The liner is then laid out and cut to job site specifications and is then ready for the resin to be prepared.
The resin is measured and mixed according to calculations made by the technician. All factors are accounted for when determining the correct mix such as ambient temperature, humidity, depth, pipe composition, etc. The solution is then combined and the clock starts. The mixing bit is attached to the drill and inserted into the mixture. The solution is mixed until all resins and epoxies are mixed evenly.
The resin system is now ready to be applied to the liner material. The mixture is poured into the liner and spread evenly throughout the liner with a roller multiple times until the liner is completely 100% saturated.
The liner is then inserted into the cooling bin and cooled to keep the epoxy from curing before it is shot into the pipe. We lift the entire wet-out liner up and quickly bring it towards the cooler we have set up on a wagon. This is so we can then transport the liner to the access point. The entire liner must be kept iced down until the last minute.
The liner is then pulled through the inversion unit and fastened inside out to the inversion unit. In this case we are utilizing a Max LinerGun™.
Prior to the inversion process the Max LinerGun™ must be connected to the control manifold which is connected to a compressor. The input pressure and output pressure are then stabilized and the inversion process can begin.
The Inversion
The liner is coated with vegetable oil to make it slippery and avoid friction. A section of liner is pushed into the gun and using the control manifold the pressure is alternated between pressurizing and depressurizing the seal tube to invert and push the liner forward. The next step is positioning the liner into the sewer line, the process is then repeated until the line is fully inverted into the pipe.
Curing of the Inverted Liners
After the installation, a calibration tube is inverted into the liner and pressurized with a compressor that is connected to the liner inflation control box. By maintaining pressure in the liner during curing, a strong bond between the liner and the pipe will result.
Finished Product
After the curing process is complete the air is released from the liner, the end and all side connections are cut out using a cutting tool. A final inspection is done with a CCTV camera and the job site is cleaned up. An installation report is generated after each liner installation. We can assist you in the selection of liners and epoxy resins as well as offer recommendations for your specific lining jobs. Contact us if you have any questions.